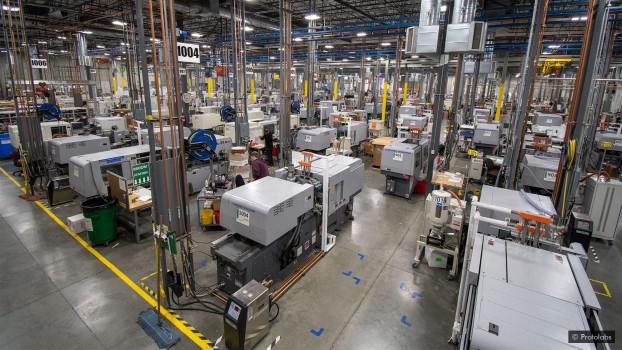
Industry news - how industries have adjusted to the pandemic in order to survive
The current situation leaves a certain (rather strong and, mainly, negative) imprint on all spheres of our life and, of course, the economy. We are interested in how production adapts to the pandemic. We share curious world experience.
In early March, the directors of London-based boutique liquor brand 58 Gin called an emergency meeting to discuss the future of their company. With government policy orders quickly shutting all doors in the UK, the mainstream market for their hand-made gin instantly disappeared.
“We suddenly had a business with no customers = income - and if we didn't do anything, we would no longer have a business,” explains managing director of the distillery Carmen O'Neill. The company made a quick and ingenious decision: they stopped distilling small-scale gin and instead started making a large-scale hand sanitizer - dubbed the "Hand Gin-itizer" - to help in the battle against Covid-19.
The key ingredients for gin have proven to be beneficial for hand sanitizer as well. “Since we already had a supply of alcohol at the distillery, we were able to denature that [alcohol] to make hand sanitizer,” says O'Neill. Note that simply pouring gin on your hands will not work, as disinfectants require at least 60% alcohol concentration, well above the 40% standard for spirits.
The example of a distillery that quickly changed production from gin to sanitizer is not the only one - it is just one of many companies around the world that are helping to fight the current pandemic. Dyson has accepted an order from the UK government for 10,000 fans instead of making machines that draw in air (vacuum cleaners). Even the Royal Mint makes plastic visors for UK medical personnel.
In France, luxury goods maker LVMH uses equipment typically producing high quality perfumes and cosmetics for Christian Dior, Guerlain and Givenchy for the Gallic sanitizer. In Japan, electronics giant Sharp has adapted its existing cleanroom manufacturing facility for LCD panels to produce 150,000 surgical masks a day. And in China, carmaker SGMW - a joint venture between US giant General Motors and two Chinese partners - began manufacturing face masks in February using medical-grade textiles from a supplier that previously supplied car interiors.
Gear shift.
Companies change their product lines for a number of reasons. In the US, the government has enforced the Defense Manufacturing Act to force some companies, such as GM, to produce ventilators. But most of the companies that have repurposed manufacturing have done so to maintain some productivity and earnings when regular orders dry up. Add to that the ability to say that they are genuinely helping in the real battle for life, with the chance to earn a reputation out of it.
Manufacturing simple hygiene and protective products is often relatively easy: firms adapt equipment, do basic research and design, and then start making face masks or hand sanitizer within days.
Take Britain's Royal Mint, which began producing plastic visors for healthcare workers in late March in addition to the coins and precious metal investment products it is known for. In the short time since the production line change, the Mint has produced 30,000 visors. “A week ago, we didn't know anything about visors, and now we make them every 10 seconds,” says Layton John at the Royal Mint.
Something like a clear plastic mask can go from design to production in a few days, but more complex parts can be made in a short time, thanks to 21st century industries using things like advanced digital design and 3D printing technology.
One of the manufacturing firms using this technology is Protolabs in Minnesota. “We made 10,000 parts for Covid-19 test kits over the weekend,” said CEO Vicki Holt. "And we have several hospitals that ask us to produce a face shield - we're talking hundreds of thousands of people we can help."
Other virus-related products on the Protolabs order book include 50,000 clips to attach to pediatric face masks, sheet metal components for Covid-19 automated laboratory test equipment, and 25 different molds for ventilators. "Doctors at the University of Minnesota have also asked to quickly manufacture six different prototype components for their low-cost ventilator to expedite FDA approval and move quickly to mass production."
Collision with obstacles.
However, such dramatic manufacturing changes are not without hurdles. Finding unexpectedly scarce materials is one of the challenges. Although the Royal Mint engineers quickly came up with a design for the visor, the purchase of large quantities of the 1mm clear PET plastic used in the visors proved to be an initial hurdle.
Obtaining the required regulatory approval for some products is another challenge. For example, past medical scandals, such as the rupture of French-made breast implants in 2010, prompted the European Union to plan new stringent medical device regulations, which were to take effect in May as a European Medical Device regulation. But European lawmakers are currently seeking to delay the passage of the law to ease the way for the production and use of emergency medical technology during a pandemic.
In the UK, the MHRA (Healthcare Products Regulatory Agency) has released details on “Minimum Acceptable” ventilator designs and has developed an exemption policy to expedite approval of medical devices during the Covid-19 outbreak.
The University of Minnesota partnered with Protolabs to produce prototype components for its low-cost Coventor fan.
An "open source" future?
As companies are forced to exchange information about the design of their products, intellectual property issues are another hurdle. For example, in the UK, organizations such as Engineers for Physicians and the Royal Academy of Engineering share resources and all the background information to help businesses create vital health products.
Some say the urgency and scale of the Covid-19 response could change the way we collaborate in the future. Technical innovation and collaboration will take a very different direction, says John Lazar, chairman of Enza Capital and a research fellow at the Royal Academy of Engineering. “Many of the rapid innovations of Covid-19 have already spread everywhere - the UCL-Ventura continuous positive airway pressure (CPAP) design is a remarkable example - and people have become much more accustomed to sensible open licenses [and] collaborative networks that cements new ways of working. ".
No wonder the word "crisis" in China consists of two hieroglyphs, meaning not only "danger", but also "opportunity."
Source - https://www.bbc.com