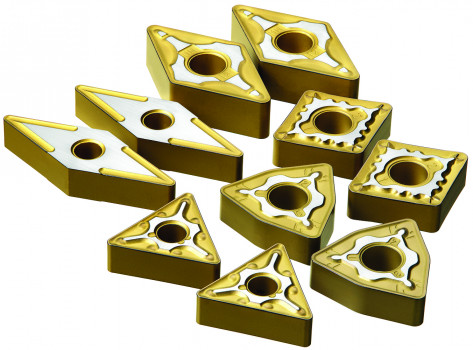
FIRST CHOICE VERSATILITY SAVES INVENTORY COSTS
MC6125 has the combination of a tough base material and new multi-layers of Al2O3 coating for improved wear resistance at high temperatures. It also has higher peeling resistance and cutting edge stability achieved by super TOUGH-GRIP technology. This provides the ultimate enhancement of the adhesion between the Al2O3 and TiCN base coating layers.
Tooling engineers and CNC machine programmers face a huge choice of turning ins ert grades and chipbreakers in the modern market place. Mitsubishi Materials has designed and developed a new grade, MC6125, that is highly versatile and can perform at the highest level across an increased range of different applications. This enables an easy first choice start point when choosing an insert for turning steels and thereby reduces the inventory levels of inserts.
This new CVD coated grade for machining a wide range of steels provides both excellent cutting edge stability and long tool life. MC6125 has the combination of a tough base material and new multi-layers of Al2O3 coating for improved wear resistance at high temperatures. It also has higher peeling resistance and cutting edge stability achieved by super TOUGH-GRIP technology. This provides the ultimate enhancement of the adhesion between the Al2O3 and TiCN base coating layers.
Super Nano Texture Technology
The outstanding crystal orientation of the Al2O3 coating has been developed by improving the conventional Nano Texture Technology. These technological improvements increase both wear resistance and tool life.
Preventing wear and sudden fracturing
Cracks that occur due to the impacts during unstable cutting are prevented by the relaxation of the tensile stress of the coating. The MC6125 grade decreases the tensile stress by 80% compared to conventional CVD inserts. When cracks are generated in the surface of coatings during machining, they propagate through in to the substrate due to the large tensile stress in the coating structure. This creates one of the main causes of sudden insert breakage. MC6125 has a much lower level of stress than conventional CVD coatings due to the surface treatment that spreads the force of impacts during machining and protects it from sudden fracturing.
A new range of possibilities
The combination of the tough substrate and wear resistant coating enables high performance during both high speed continuous and interrupted cutting, thereby permitting a wider range of steel turning applications from medium through to high cutting speeds.
The inserts are finished in a gold colour for easy identification of used edges and are available in 6 negative geometries, CNMG, DNMG, SNMG, TNMG, VNMG and WNMG, with 11 different chipbreakers.