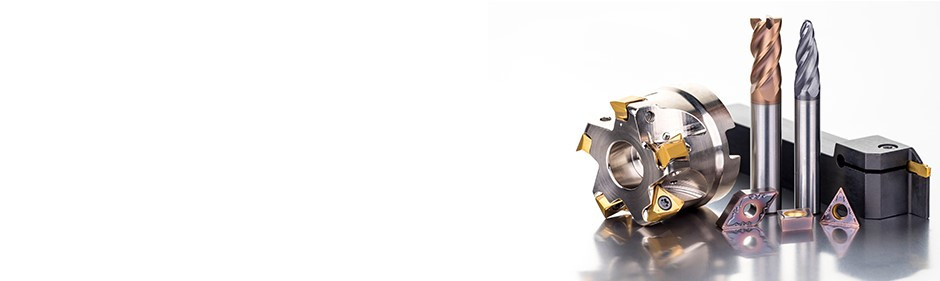
The future is already here
To expand the technological capabilities and gain an additional advantage in metalworking, our company has created a new tool for turning and milling operations:
-
new five-pronged monolithic milling cutters;
-
expanding the range of tools for grooving and cutting;
-
milling cutters for processing non-ferrous alloys;
-
parabolic milling cutters;
-
milling cutters with TNGX plates for processing ledges;
-
a new generation of hard alloy for turning.
New generation of five-prong milling cutters
The new generation of solid carbide cutters with five teeth has been specially created for dynamic milling of workpieces in the conditions of general processing, production of dies and molds.
The S7 series cutters can be used for a variety of operations and in a variety of workpiece materials, including stainless steels and heat-resistant alloys.
The new S770HB, S771HB, S772HB and S773HB milling cutters offer up to 25% higher productivity compared to four-tooth milling cutters. The positive front angle ensures smooth cutting in stainless steel and heat-resistant alloy workpieces, which reduces the risk of hardening the work piece. The AlCrN coating helps to reduce the coefficient of friction, increase the thermal stability of wear resistance.
The small rounding radius and the special design of the cutting edge allow you to ensure stable performance, reduce the risk of chipping edges and increase tool life.
The S771HB and S773HB cutters can be used for various operations: profiling, trochoidal milling, semi-finishing and narrow pocket milling. These milling cutters have chip-breaking grooves for crushing chips, which reduce the load on the spindle, increase the volume of material to be removed and increase the milling width by 50% compared to a tool without chip-breaking structural elements.
The cutter neck of the smaller diameter prevents contact with the wall of the workpiece to be processed, and the internal coolant supply increases the efficiency of milling difficult-to-process materials.
The S770HB and S772HB milling cutters are more suitable for trochoidal milling, profiling and semi-finishing operations with maximum productivity due to the increased volume of material removed and reduced main processing time.
In addition, there are three types of universal high-performance milling cutters for use both on CNC machines and on machines with manual control.
The S722HB, S765HB, and S768 milling cutters can be used for most operations, such as grooving, plunging, contouring, angling, and copying most workpiece materials, including structural and stainless steels, as well as heat-resistant alloys.
The four-tooth milling cutters have a special cutting part design for improved chip removal. AlCrN and TiSiN coatings increase the wear resistance and redness of the tool, allow you to process workpieces with a higher cutting speed, which is ideal for processing without coolant.
The range of milling cutters for processing materials with a hardness above 49 HRC is complemented by the new S561 milling cutters, which are capable of performing high-performance processing in various industries, including the production of dies and molds.
These four-tooth cutters also have a special design of cutting edges for improved chip removal and allow you to get a high quality of the processed surface of the workpieces made of hardened steel with a hardness of 52...70 HRC. The special end sharpening of each tooth increases the strength and resistance to chipping during milling.
Grooving and cutting process
The tool for processing deeper grooves and GL segments is supplemented with new holders, long double-sided plates and new geometries. The new tool expands our range with the possibility of copying and longitudinal turning of various materials in conditions of application with a small departure and processing of small workpieces.
The expansion of the range continues after the introduction in 2019 of new holders and extended GL plates with the new G8330 alloy, which has a PVD coating.
The new addition includes 12x12 cross-section holders for additional processing operations with plates of different widths. The reinforced design of the plate attachment provides high rigidity and vibration resistance, which allows you to get a high-quality treated surface.
Time savings can be achieved when installing the plates thanks to the convenient access to the clamping screw (at an angle of 30°) and the ability to replace the plate with one hand.
The new GLSF (RL) EXT universal holders have a reach of 24...32 mm, holders GLSF (RL) EXT-G - 10...12 mm. The GLSF (RL) EXT-S holders can be used for processing small parts and on bar lathes.
The double-sided extended GL plates allow for up to 60% deeper grooving compared to the standard LCMF16 plate range. The new positive MM and GM geometries have higher durability, reduced cutting forces, and a lower chance of build-up.
The MM geometry has a rounded cutting edge for copy turning. The GM geometry is designed not only for radial grooving, but also for longitudinal turning.
Wider plates (up to 6 mm) are available for processing small workpieces. The design of the plates with a geometry of MM with a width of 5 mm and 6 mm does not require modification of the holder for deeper processing. All new plates are available in CVD-coated T7325 and PVD-coated G8330 alloys for processing most billet materials.
Milling of non-ferrous alloys
The range of S6 carbide end mills for processing non-ferrous alloys is complemented by new three-and four-tooth end mills, as well as small diameters of existing two-tooth end mills.
The S6 series milling cutters are suitable for precise and high-speed processing of aluminum alloy workpieces in the aerospace and automotive industries, as well as in the production of dies and molds.
The three-tooth designs (S650, S614 and S654) ensure smooth cutting and low spindle load. The four-tooth (S662) cutters have different rounding radius values, which increases the strength of the cutting edges and the stability of the machining.
The variable pitch of the teeth allows you to reduce the likelihood of vibration, increase the durability and productivity of the tool. The positive front angle ensures smooth cutting, which reduces the risk of hardening of the workpiece.
The smaller diameter S654 cutter neck prevents contact with the wall of the workpiece to be processed. The NRA profile is designed for efficient chip crushing, reducing the load on the spindle and increasing the volume of the material to be removed.
Parabolic milling Cutters
The new parabolic milling cutters allow efficient five-axis machining in the aerospace industry, in the production of dies and molds.
The new S791 milling cutters provide excellent surface quality and are suitable for semi-finishing and finishing workpieces made of structural and stainless steels, cast iron and heat-resistant alloys. The design of the milling cutters has a combination of a spherical top and a side surface of a large radius for smooth processing of shaped surfaces and walls with minimal differences.
The large radius of the side surface of the cutter for processing the walls of workpieces with a wide overlap allows you to increase the contact surface with the workpiece, increase tool life, reduce the number of passes and save up to 50% of the processing time.
According to the results of one of the last tests, the surface of the workpiece was processed in 18 passes when using a parabolic cutter and in 36 passes when using a spherical cutter under the same conditions.
Minimal differences on the treated surface after using the S791 parabolic cutter allow you to reduce the time and cost of subsequent operations. The positive front angle of the cutter ensures smooth cutting in stainless steel and heat-resistant alloys, which reduces the risk of hardening of the workpiece.
The AlCrN coating creates thermal stability, reduces the coefficient of friction and increases the wear resistance of the tool. Different versions of parabolic cutters with three or four teeth have higher productivity (compared to conventional spherical cutters with two teeth).
For more information, please contact your local Dormer Pramet representative and follow the updates on social networks.
Ledge milling
Ledge cutters with a 90° plan angle are complemented by STN16 designs with larger TNGX16 plates, which allow you to work at a large cutting depth (up to 10 mm) with a higher feed rate. Triangular plates have six cutting edges, which allows you to get a high economic advantage.
Reduced cutting forces create smooth and quiet processing, which guarantees high process safety. The low cutting resistance allows you to minimize the amount of irregularities between the passes for precise milling of vertical walls to obtain excellent quality surfaces.
The positive geometry and internal coolant supply contribute to efficient chip removal when processing a wide range of materials to be processed, including structural and stainless steels, cast iron, and non-ferrous alloys.
The range of TNGX16 plates allows you to choose a different radius at the top from 0.4 mm to 1.6 mm, suitable alloys and chip-breaking geometries F, M or FA.
The F geometry is the first choice for processing low-and medium-carbon steels. A particularly positive geometry with a narrow peripheral chamfer allows you to apply this geometry in conditions of semi-finishing and finishing.
The M geometry is suitable for processing carbon steels, standard stainless steels, and cast iron. The medium-sized positive chamfer allows you to apply this geometry in semi-finishing and finishing conditions.
The FA geometry is suitable for processing non-ferrous alloys. This geometry has a particularly positive geometry and is made in combination with an uncoated hard alloy. The polished front surfaces significantly reduce the likelihood of sticking of the processed material.
The STN16 milling cutters have a fairly large number of teeth for increased productivity and a variable tooth pitch design for smoother machining (starting from a diameter of 50 mm).
The milling cutters are made of coated tool steel to increase corrosion resistance and reduce friction. Large and strong screws increase the reliability of the structure and facilitate the installation of plates. Precisely machined seats ensure tool interchangeability and reliability after changing plates.
New generation of hard alloy
The advanced hard alloy T8330 has received a new generation of PVD coating, which has improved the wear resistance and performance of the turning plates.
The new T8430 alloy is versatile for most turning operations, including heavy roughing. Designed for turning structural steels, this hard alloy is also well suited for stainless steels, cast iron, and heat-resistant alloys. A significant increase in wear resistance compared to existing hard alloys allows you to successfully cope with untreated steel workpieces and other hard-to-work materials (heat-resistant alloys, Inconel and Stellite).
The multi-layer PVD coating of the new alloy, optimized for increased performance, has improved durability by up to 69% compared to the T8330. The unique TiBN top layer reduces the chance of build-up and increases productivity. A thick TiN coating with low internal stresses contributes to increased resistance to crater wear. The solid layer of AlTiN provides high abrasion resistance on the back surface of the plate.