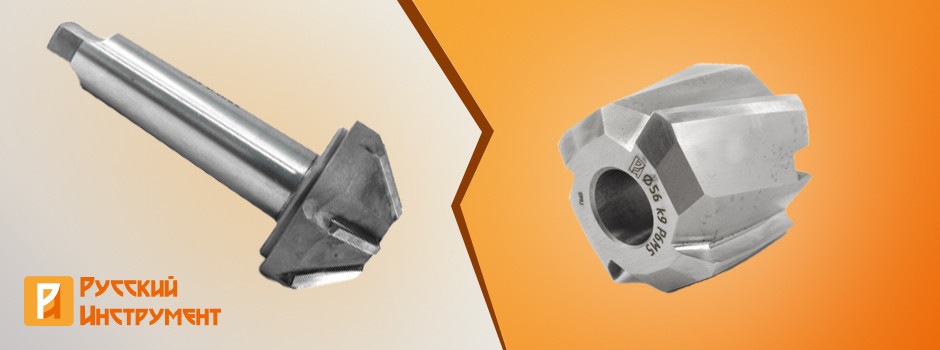
Countersink and Countersink. Purpose and scope of application
In the modern world of mechanical engineering and construction, where quality and precision play a key role, the use of countersink and countersink becomes an integral part of the machining process. These two terms, although they have some similarities, actually refer to two different metalworking operations. We will take a detailed look at each of them to help you better understand their specifics and application possibilities.
Zenker
A countersink is a metal–cutting tool that is used to prepare a hole for processing. To obtain a hole and tighten bolts and nuts in a metal part or workpiece, it is not enough to perform a drilling operation and cut the thread. An important step will be the preliminary cleaning of the surface from irregularities and burrs, creating the required shape.
Purpose and scope of application
The main purpose of the product is to improve the surface quality of the drilled hole. With the help of a countersink, you can change the level of roughness, increase grip, adjust the diameter and geometric shape, calibrate the hole for fasteners, get rid of defects.
Speaking about the difference between a countersink and a sweep, it should be emphasized that countersinking is, first of all, an increase in the size of the hole and semi–finishing, and deployment is finishing.
Metal-cutting countersink is widely used both in everyday life and in industry. Amateur craftsmen use countersinks as a nozzle for a drill and a screwdriver. At industrial enterprises, the countersink is used as a tool for various types of machines (turning, drilling, milling, aggregate, etc.).
Design features
The design of the countersink is similar to a drill, you can distinguish the countersink by the available cutting elements. Among the main elements of the countersink are:
- cutting working part – teeth and edges;
- the neck separating the shank from the cutting part;
- the tail part intended for fixing the tool.
How does the tool work?
After turning on the machine and starting the engine, the countersink begins to perform translational rotational movements, cuts off the metal layers with the cutting part, going deeper into the workpiece, while simultaneously cleaning the surface of the hole.
Material of manufacture
For the production of countersinks, high-speed tool grades of steel P6M5 or P18 are used. When working with this type of tool, cooling agents are used on machines to reduce the processing temperature and protect the tool, as well as lubricants to reduce the friction force and remove chips.
The tool is standardized, manufactured in accordance with GOST 12489-71.
Advantages of the countersink
- Strength and durability.
- High-quality and precise surface treatment regardless of their hardness.
- Simplicity and reliability of the design.
- The ability to quickly install and replace the snap-in.
Classification of countersinks
The instruments are classified according to various parameters. Let's consider the main types of metal countersinks.
According to the method of fixing on the machine:
- solid or tail – have a single design with cutting edges and grooves for chip removal, the shank has the shape of a cone,
- attachment – equipped with an internal hole, with which the attachment to the mandrel of the machine is carried out.
By the shape of the recesses:
- cylindrical – used to obtain holes and recesses of cylindrical shape. Their working part is supplemented with special guides (trunnion), which allows you to prepare holes for mounting fasteners,
- conical – for processing holes in the form of a cone,
- end–mounted - used for processing transverse surfaces, the working part of such countersinks is located on the end side. With their help, you can clean the holes from protruding parts (bosses and tides) left over from previous operations.
By design: solid, prefabricated, welded, with carbide plates.
In the direction of rotation of the grooves: left and right.
Countersinks also differ in the number of edges, steel grades and other parameters.
When choosing a tool, you should consider what kind of work it is needed for. The technical characteristics of the countersink will depend on this: diameter, length of the working part, shape of the shank, material of manufacture, quantity and quality of cutting edges.
Countersinks Russian Instrument on Enex
Countersink
Countersinking is the process of forming depressions for the heads of fasteners (screws, rivets, nuts) or processing holes for deburring. A conversation about what hole countersinking is would be incomplete without mentioning that the tool is also used for cutting internal chamfers. The process is performed using a special metal-cutting tool called a countersink.
The production of countersinks is carried out according to GOST 14953-80. Hard-alloy materials, steel alloys, as well as high-speed types of steel are used for manufacturing. Let's consider what the countersink is for.
Scope of use
In metalworking, the use of countersinks is necessary to create holes to ensure an accurate and strong connection between two metal elements, to create a recess for bolts, screws or rivets, etc.
What is the difference between a countersink and a countersink?
According to GOST, both countersink and countersink are used for hole processing. At the same time, a distinctive feature of the countersink is the presence of a conical working part, which allows you to obtain the necessary support planes and conical recesses of a given length.
Design features
The countersink design consists of a rod with a cut tip in the shape of a cone. This form is the most common, as it allows you to get a smooth deepening. The countersink angle determines the shape and depth of the recess. Standard angles from 60° to 120° are usually used, although there may be other parameters depending on the requirements of the project. The countersink has cutting edges that remove material and form a conical shape. The edges must be sharp and precise to ensure a high-quality result. Their number varies from 6 to 12. The depth of the countersink determines how deeply the screw, nail or other fastener will be immersed. The depth should be sufficient to create a strong and reliable connection, but not so deep as to weaken the material or damage its structure.
Types of countersinks
There are several types of countersinks that differ in shape and size. The classification of countersinks is based on the types of equipment used, the configuration of the cutting part, the diameter of the hole.
So, depending on the type of machine on which the processing is performed, the countersink can form recesses and support planes, chamfer, process holes for fasteners.
Depending on the configuration of the cutting part, cylindrical, conical, and end tools are distinguished.
Depending on the diameter of the hole that is being processed, there are simple countersinks (0.5-1.5 mm.), tools for working with holes up to 6 mm., as well as countersinks for holes whose diameter exceeds 12 mm.
Countersinks Russian Instrument on Enex
The full catalog of the company "Russian Instrument" on Enex