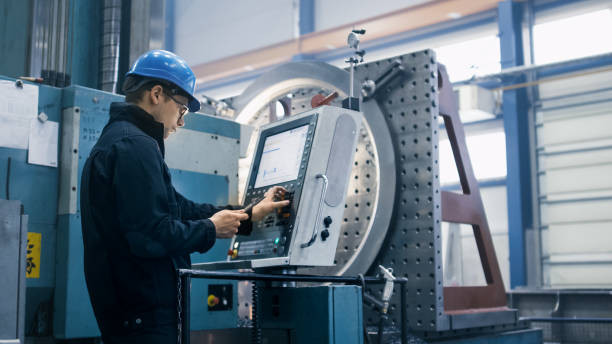
Overview of the machine tool market
Continuing to review the various segments of the industrial equipment market, we would like to turn today to machine tools. Consider the trends that have emerged in recent years and evaluate the newly opened prospects. We present you the latest data for 2022!
A metal cutting machine is a machine designed to process workpieces in order to form specified surfaces by removing chips or by plastic deformation. Processing is carried out with a cutting or abrasive tool.
Classification of machines - what are they?
All metalworking equipment is classified according to certain characteristics, depending on the type of technological process, cutting tool, machine layout.
Metal-cutting machines, depending on the nature of the work performed and the type of cutting tools used, are divided into 11 groups:
The group of lathes (pos. 1 - 6) consists of machines designed for processing surfaces of rotation. The unifying feature of the machines of this group is the use of the rotational movement of the workpiece as a cutting movement.
The group of drilling machines (pos. 7 - 10) also includes boring machines. The unifying feature of this group of machines is their purpose - the processing of round holes. The cutting motion is the rotational motion of the tool, which is usually also accompanied by a feed motion. In horizontal boring machines, the feed can also be carried out by moving the table with the workpiece.
The group of grinding machines (pos. 20 - 24) is combined on the basis of the use of abrasive grinding wheels as a cutting tool.
The group of polishing and finishing machines is united on the basis of the use of abrasive bars, abrasive belts, powders and pastes as a cutting tool.
The group of gear-cutting machines includes all machines that are used to process gear teeth, including grinding machines.
The group of milling machines (pos. 11 - 14) consists of machines that use multi-blade tools - milling cutters as a cutting tool.
The group of planers (pos. 15 - 17) consists of machines in which a common feature is the use of the rectilinear reciprocating movement of the cutter or workpiece as a cutting movement.
The group of cutting machines includes all types of machines designed for cutting and sawing rolled materials (rods, angles, channels, etc.).
The group of broaching machines (loz. 18 and 19) has one common feature: the use of special multi-blade tools - broaches as a cutting tool.
The group of threading machines includes all machines (except machines of the turning group) designed specifically for the manufacture of threads.
Machine tools are classified according to many criteria
Classification of machine tools according to the degree of specialization:
universal. For the manufacture of a wide range of parts in small batches. Used in single and serial production. Also used in repair work;
specialized. For the manufacture of large batches of parts of the same type. Used in medium and large-scale production;
special. For the manufacture of one part or part of one standard size. Used in large-scale and mass production.
Classification by degree of accuracy
The degree of processing accuracy on this machine is indicated by the letter included in its designation:
H - normal accuracy;
P - increased accuracy;
B - high accuracy;
A - especially high accuracy;
C - especially precise master machines.
Mass classification
Depending on the mass of manufactured parts, machines are divided into:
light, weighing up to 1000 kg;
medium, weighing up to 10,000 kg;
heavy, weighing from 10,000 kg, which, in turn, are divided into large (16,000-30,000 kg) and actually heavy (up to 100,000 kg);
especially heavy - over 100,000 kg.
Classification of metal-cutting machines according to the degree of automation:
manual;
semi-automatic;
automatic machines;
CNC machines;
flexible production systems.
The volume of the global machine tool market in 2020 amounted to 111.36 billion US dollars. The global impact of COVID-19 has been quite severe, with demand for machine tools declining in all regions amid the pandemic. According to the analysis, the global market showed a decline of 1.3% in 2020 compared to the average year-on-year growth in 2017-2019. The market is projected to grow from $113.26 billion in 2021 to $164.92 billion in 2028 at a CAGR of 5.5% over the period 2021-2028. The sudden rise is attributed to demand and the growth of this market, which returns to pre-pandemic levels after the end of the pandemic.
TGM invests in CNC machine toolsThe production of machine tools has been influenced by the demand for them in automotive, industrial and transport technology. In addition, suppliers are focusing on the digital transformation of equipment due to the transition of the era from conventional to CNC machines. This transformation is the result of demand for high performance, high quality and reduced cycle times in the end user industry. For example, in August 2020 TGM Ltd. invested US$1.43 million to launch CNC technologies to target major aerospace and defense companies. With the introduction of these new technologies, the company expects to double its sales in just two years. Likewise, the growth of CNC machine tools is expected to increase significantly over time across all end-use industries.
Growing demand for smart machines is a notable trend
Technological advances such as the increasing adoption of robotics, human-machine interaction are observed to be driving the growth of the market in the current period. The requirement to connect to the cloud in real time is another trend in advanced manufacturing. Thus, hardware is becoming a vital part of intelligent systems and is becoming more and more popular. These smart tools are equipped with sensors to optimize machine time and schedule maintenance. This data can be analyzed and help improve performance. In addition, sensors can improve the predictive analysis of the tool and its life cycle. It is expected that this will reduce downtime and help to significantly solve the problems associated with equipment shutdown. In addition, the rapid adoption of smart features such as lower power consumption is expected to boost the market in terms of revenue.
Growing adoption of additive manufacturing (“3D printing”) and hybrid machines to increase demand
New Okuma Laser EX machinesGrowth in additive manufacturing is driving the market. Manufacturers are shifting to leaner and faster manufacturing processes, which in turn is leading to greater adoption of additive manufacturing. In addition, the growing popularity of heterogeneous material manufacturing capabilities is expected to lead to market growth. CNC manufacturers are planning to introduce additive manufacturing into their business. For example, Okuma plans to introduce its new Laser EX machines in the future, which will include laser hardening of carbon steel material, as well as laser heating and self-cooling hardening. Thus, such innovative combinations of technologies are expected to drive the growth of the market in the future.
Uncertainty related to social and economic factors hinders the growth of the market
AutomotiveIndustryChanges in global economic conditions lead to a slowdown in market growth. Manufacturing costs are directly proportional to the sales of these tools. Therefore, if the global economy slows down, it is expected that this will directly lead to lower machine tool revenues. Similarly, trends in the automotive industry have had a greater impact on the tool sector due to the widespread adoption of machines in the industry. However, capital expenditure trends in the automotive sector have a significant impact on market revenue. In addition, unexpected changes in the economic, political or social circumstances of a country can affect the growth of market income.
Digital transformation of machine tools meets the demand for CNC machines
Depending on the technology, the market is divided into machine tools with numerical control (CNC) and traditional ones.
CNC machine toolsThe CNC machine tool segment is expected to drive the market in the near future due to the growing demand for process automation in various industries. Increasing automation of manufacturing processes due to growing demand for increased accuracy and short lead times is expected to lead to market growth. Thus, the key players have focused on the development of CNC systems to meet various industrial requirements.