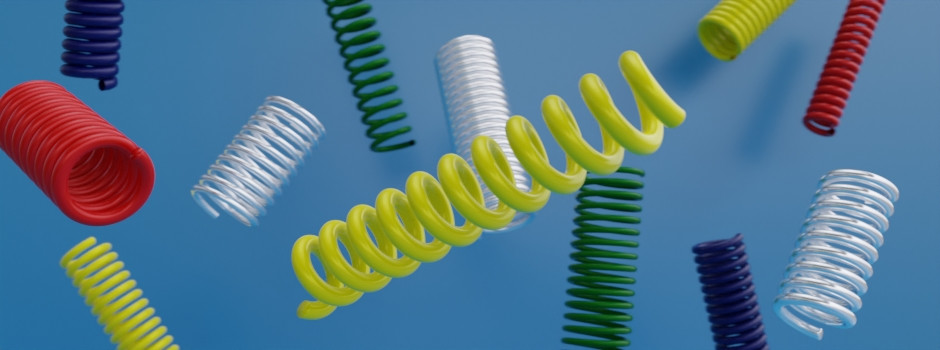
Methods of winding Stamo springs
Stamo manufactures springs of any complexity and configuration, using various curling methods using the latest equipment.
Production of cold wound springs
The method of cold winding flat or helical springs is the most common. For this, lathes or special program-controlled spring-coiling machines are usually used. Manual winding is also possible, but this method is used only when it is necessary to produce parts individually or in very small batches.
The process of cold winding of helical springs on machines has certain stages:
- first, a visual inspection of the wire is carried out and it is straightened to identify delaminations and other defects;
- then the cold bar is wound on a special mill, cut and finished;
- in some cases, procedures are carried out for hardening and tempering the finished product to relieve the internal stress of the metal;
- after that, the spring can be electroplated, depending on the purpose of the product.
As you can see, some stages are not mandatory, and their presence is largely determined by the technological parameters of the future spring.
The method of cold winding springs has a number of disadvantages:
- it is only suitable for wire diameter up to 16mm;
- skipping the product dispensing phase may have a negative impact on product quality;
- bars that are too hard may break when cold coiled.
At the same time, these shortcomings are compensated by one important advantage - the comparative cheapness of the method and, as a result, its prevalence.
Production of hot coiled springs
The method of hot winding in the manufacture of helical springs is not so popular, and the reason for this is the high cost of equipment, which not all Russian enterprises can afford.
The main difference from the cold winding technology is that the wire is heated and fed to the winding mill in a hot state. The main steps of the hot winding process are as follows:
- cutting and heating the workpiece;
- processing of the ends of the workpiece - guy or rolling;
- reheat;
- winding the spring and trimming the ends;
- wiring and editing the spring;
- hardening and tempering of the product;
- end grinding;
- coating depending on the operating conditions of the spring.
This method involves more steps and requires special equipment, so it is more laborious and expensive. High cost is the most significant disadvantage of hot winding, but it is offset by significant advantages:
- you can use wire with a diameter of 10mm or more;
- the technical characteristics of the springs are better than with the cold winding method.
The production of springs by hot winding opens up a wide range of possibilities for engineers, allowing the design of mechanisms with large springs, not limited to a wire diameter of 16mm.
STAMO manufactures its coil springs using both cold and hot winding methods, with all the necessary equipment for this. Thus, we can offer our customers springs with wire diameters up to 80 mm. Such springs have few analogues in Russia and are used in large mechanisms or in units of units operating under high loads.