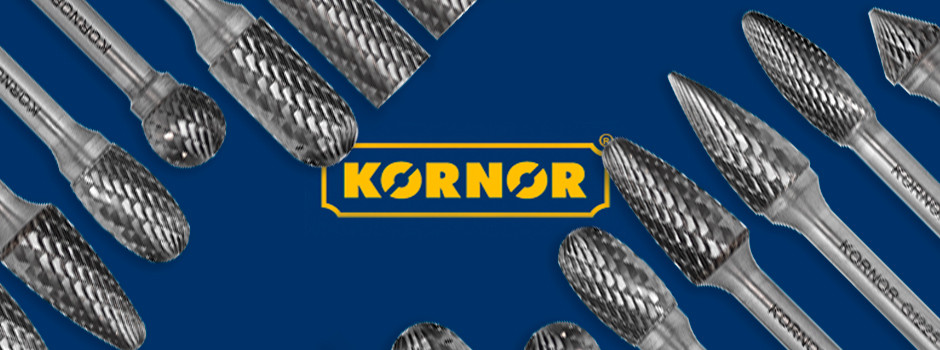
What are carbide boreholes, their types and where are they used
A borehole cutter is one of the types of metal–cutting tools, it is a pin with a carbide head, which is used for processing various materials - steel, titanium, cast iron, non-ferrous metals, graphite, glass and plastic. Boreholes (metal balls) come in a wide variety of types, exactly what configuration such a milling cutter will be depends on the scope of its application.
The durability of boreholes and high wear resistance have allowed them to be widely used both in production and in private workshops, where they have successfully replaced traditional files. Thanks to the hard alloy, boreholes can maintain their performance characteristics for a long time, even when working in the most difficult and extreme conditions.
Unlike abrasive grinding heads, the cutting part of the boreholes is made of a hard alloy, usually tungsten carbide (VK, VK8). Thus, the performance and resource of such boreholes are significantly higher. Boreholes made of hard alloy are more than twice as productive and resource-efficient as boreholes with heads made of high-speed steel.
Using boreholes:
-
they level the surfaces;
-
welds are processed;
-
bore the holes to the desired size;
-
shaped holes are cut out;
-
the edges and burrs on the workpieces are ground.
-
engraving is carried out.
Depending on the nature of the work, the following types of boreholes are distinguished:
-
Cylindrical, type A
-
Cylindrical with an end face, type B
-
Spherical cylindrical, type C
-
Spherical, type D
-
Oval, type E
-
Hyperbolic with a spherical end, type F
-
Hyperbolic with a point end, type G
-
Flame-shaped, type H
-
Conical 60°, type J
-
Conical 90°, type K
-
Spheroconic, type L
-
Conical, type M
-
Reverse cone, type N
Appearance of the borehole:
![]() |
![]() |
![]() |
![]() |
A = Cylindrical | B = Cylindrical with an end | C = Spherical cylindrical | D = Spherical |
![]() |
![]() |
![]() |
![]() |
E = Oval | F = Hyperbolic with spherical end | G = Hyperbolic with a point end | H = Flame-shaped |
![]() |
![]() |
![]() |
![]() |
J = Cone with an angle of 60 degrees | K = Cone with an angle of 90 degrees | L = Spheroconic | M = Conical, pointed |
|
![]() |
||
|
N = Reverse cone |
Also, carbide boreholes differ in the types of notching (sharpening), let's consider the main ones:
-
Double notch - effectively removes the material, forms fine chips, and is successfully applied to most materials. It is used in finishing operations
-
Single notch –effectively removes the material, maximizes the use of the tooth profile, produces long chips. General application.
-
Large notch – for non-ferrous metals, maximum removal of material in the absence of sticking, excellent for non-ferrous metals and plastics.
Kornor company offers a wide range of products carbide boreholes. In addition, in Kornor catalog you will find a large selection of accessories and accessories for metalworking and more.